HOUSING CRISIS: Kelowna factory builds economic, sustainable modular homes
When most people think of assembly lines they think of cars, toys or things you find on a department store shelf. A factory in Kelowna has an assembly line for houses that builds them quickly, sustainably and economically.
SRI Homes is a company that manufactures modular homes. The process starts with an interested buyer who picks a floor plan, and then they can choose from a laundry list of add-ons like skylights and French doors to personalize their home.
“Not only are we in a housing crisis, but we have an affordability issue as well. And modular construction actually fixes both of those. Not only is it more cost effective, but it's way faster,” SRI’s general manager Darren Bassett said.
SRI Homes has a factory on the edge of Kelowna that can build a modular home from start to occupancy in two months.
The factory works just like an assembly line for a car. It starts with the floor, then it slides down the line and gets walls, a roof, electrical and all the bells and whistles a homeowner could want, down to the towel holder in the bathroom.
There are 140 workers who are building roughly 250 homes a year, but the factory’s production manager Derek MacLeod said they could easily expand and build more than 600 homes annually.
“We’re behind the times,” MacLeod said.
Bassett said there is some prejudice against manufactured homes, but people are coming around.
“The biggest thing is just the stigma and education with all levels of government and the public,” Bassett said.
READ MORE: 'Things were built better': Kamloops and the Okanagan's best heritage listings
A major challenge for modular homes is regulation, but that might change soon. SRI hosted a task force of B.C. mayors on Nov. 22 who want to make it easier for modular homes to rollout across the province.
The Ministry of Housing announced in September that standardized designs will help cities and builders move quickly through approval processes to get people into modular homes faster.
“We've spent a lot of time educating government officials on the benefits of modular through our Modular Home Association of BC... as well as other avenues,” Bassett said.
The other challenge is transporting an entire house from the factory to a site, especially to dense neighbourhoods in the city. Bassett said sometimes craning the home onto the lot can cause disruption, but it’s still less hassle for neighbours than a long-term construction site.
“When people think about modular homes or manufactured homes, they think of trailer parks or trailer homes, which is true,” he said. “But once it gets set up on site, you wouldn't know whether that was a site built home or it actually was built in a factory. That's how similar they are from a look and a quality perspective.”
READ MORE: Survey finds huge majority of British Columbians say homeownership now a luxury
The factory in Kelowna can build a standard single family home, but it can also make modules that fit together like blocks to build ski chalets, hotels, work camps, multi-family homes and commercial spaces.
SRI Homes can build a house for as little as $125,000, then it goes through a retailer, and finally delivered to the lot where it gets hooked up to utilities.
MacLeod said people can own a basic modular home for as little as $500,000 including the price of the land. The benchmark price for a single family home in Central Okanagan is $983,000, according to the Association of Interior Realtors.
“There's a fair amount of environmental advantages as well in terms of waste of materials and that sort of thing. So, it's a greener way of building,” Bassett said.
MacLeod spent years on construction sites before working for SRI Homes. He said on a typical construction site 15 per cent of building materials go to waste. At SRI he said he’s unhappy if more than two per cent of their materials go to waste.
The materials are kept indoors until the house is sealed and weather proofed which helps reduce waste. The scrap pieces are also kept out of the elements which helps SRI reuse pieces that would normally go in the garbage.
“People are starting to understand the benefits of modular in terms of speed, quality, and cost. It is much more advantageous in comparison to a site build. And that doesn't even include the environmental advantages that you have with it, and the fact that it actually meets the national and the B.C. building code,” Bassett said.
To contact a reporter for this story, email Jesse Tomas or call 250-488-3065 or email the editor. You can also submit photos, videos or news tips to the newsroom and be entered to win a monthly prize draw. Find our Journalism Ethics policy here.
We welcome your comments and opinions on our stories but play nice. We won't censor or delete comments unless they contain off-topic statements or links, unnecessary vulgarity, false facts, spam or obviously fake profiles. If you have any concerns about what you see in comments, email the editor in the link above. SUBSCRIBE to our awesome newsletter here.
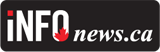